Cuando se trata de alojar unidades de pequeñas dimensiones o escaso peso, se suelen plantear dos tipos de problemas:
- Por una parte, existe un elevado número de referencias, o lo que es lo mismo, hay una gran variedad de unidades que clasificar.
- Por otra parte, es necesario obtener gran índice de rotación.
En esta sección se busca definir los parámetros que se deben tener en cuenta para conseguir una bodega de pequeñas piezas casi perfecta. El medio para alcanzar esta premisa de la manera más eficiente y racional posible es la automatización de los procesos. Sin embargo, no se debe olvidar nunca que cuando se diseña una bodega, sobre todo si es robotizada, se debe tener en mente que el costo de la instalación ha de estar proporcionado al costo total de la operación. En otras palabras, se ha de conseguir un equilibrio entre costo y utilidad.
Para lograr estos objetivos es preciso analizar cada una de las opciones de las que disponemos en una bodega con este tipo de piezas.
Principios clave para la instalación de una bodega de piezas pequeñas
Cuando se trata de planificar una instalación de este tipo, existen dos estrategias básicas claves, entre las que hay que elegir una o conjugar ambas que son planteamiento hombre a producto (es el operario el que se mueve) o producto a hombre (en el que es la carga la que se mueve hacia la posición del operario).
No existe una única solución estándar o ideal a la hora de elegir entre estos dos planteamientos. Hasta es posible que realmente no exista una solución óptima o que la decisión más adecuada sea una combinación de ambas. Esta es una cuestión de difícil respuesta, ya que nuestras estrategias se deben adaptar a cada producto y a cada industria en particular y no generalizar
Este manual busca dar una información introductoria sobre estos temas, pero recuerde que la colaboración de profesionales especialistas en la materia es imprescindible puesto que cada caso particular es diferente y no se puede generalizar sin haber realizado un estudio detallado del proyecto. Partiendo de esta premisa, a continuación procederemos a examinar las opciones que la industria especializada puede ofrecer.
1. La estrategia de hombre a producto
El principio de hombre a producto es el más convencional y clásico de los existentes. En esta modalidad, los productos son almacenados en racks colocados de diversas maneras en función del sistema elegido. La manutención de estos elementos se realiza de forma manual –y el producto se ubica pieza a pieza– o mecanizada, para lo que se manipulan unidades de carga completas, generalmente cajas o contenedores.
- Su mayor desventaja es su alto costo de manipulación
- Su ventaja fundamental es el bajo costo de su inversión.
La extracción de las unidades se lleva a cabo, normalmente, de modo manual, para lo cual el operario se ha de desplazar andando o montado sobre una máquina hasta el lugar donde está colocada la referencia que ha de buscar según la orden de pedido que ha recibido.
Los sistemas que se usan en este planteamiento son los racks en una planta, en varias plantas (mediante el uso de entreplantas o altillos), los racks sobre bases móviles, las bodegas de pasillo estrecho y los racks carton flow.
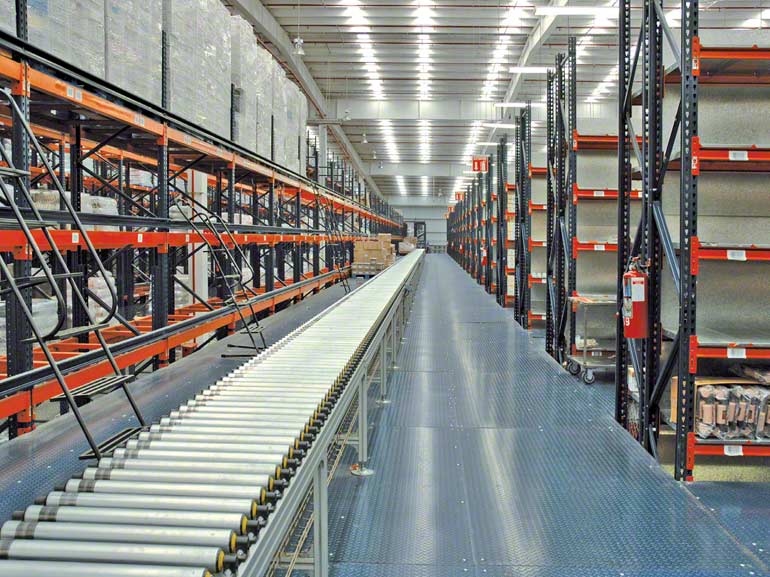
Instalación para una cadena de tiendas de autoservicio
El grado de automatización en estos sistemas es muy bajo y depende de las características propias de cada aplicación. Solo el sistema de carton flow dotado de dispositivos pick-to-light alcanza un grado importante de automatización y el empleo de carros con put-to-light.
No todos los sistemas que responden al principio hombre a producto son exactamente iguales. Para analizarlos hemos optado por puntuar las diversas opciones siguiendo la utilización de una escala del 0 al 10, aplicada a cuatro parámetros que son:
a) El costo total de la inversión
b) El costo de manipulación en términos de mano de obra (el costo del manejo por artículo, que es independiente de la inversión)
c) La capacidad de manipulación en número de movimientos por unidad de tiempo
d) El índice de utilización de la superficie en términos de uso efectivo.
A continuación procederemos a analizar uno por uno los sistemas que utilizan la estrategia "de hombre a producto" según estos cuatro parámetros.
-
Racks en una sola planta
Este tipo de racks, que generalmente son de pequeña capacidad de carga, se distribuyen en la bodega dejando un pequeño pasillo para el paso del operario y el carrito de picking. Actualmente existen sistemas muy sofisticados con gavetas de muchos tamaños y disposiciones que se adaptan a todos los volúmenes de producto y a todas las actividades industriales.
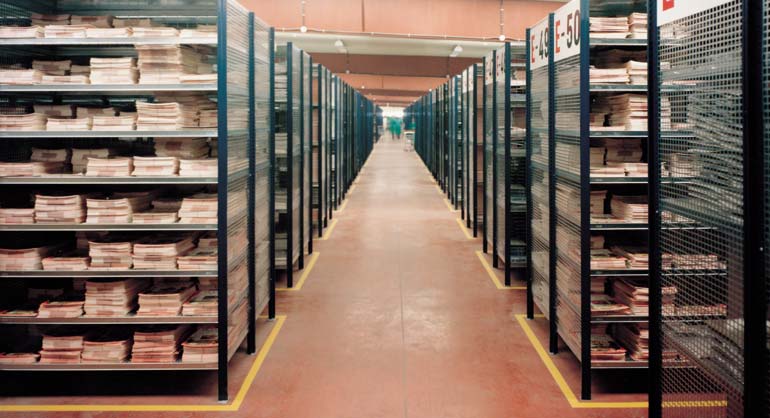
Instalación para el sector editorial
Usualmente los niveles bajos se dedican a alojar los productos de más peso y estos racks no suelen ser muy altos. Esta característica dependerá de las necesidades de cada industria y cada bodega, pero conviene tener en cuenta que las estructuras muy altas dificultan el acceso rápido a los productos situados en los puestos más elevados. Incluso, en ocasiones, se necesitan escaleras o carros-escalera, casi siempre manuales, que ralentizan el proceso de toma y colocación de las unidades.
En las bodegas dotadas de estos sistemas también se pueden emplear otros medios mecanizados como transpaletas manuales o autopropulsadas, así como preparadoras de pedidos de bajo o medio nivel (para más información, no dude en consultar el artículo referente a los equipos de manutención).
Calificación de este sistema:
Parámetro | Calificación | Comentario |
Costo total de la inversión |
1 |
Bajo |
Costo de manipulación | 8 | Alto. Por lo general, se realiza de manera totalmente manual. |
Capacidad de manipulación | 4 | Término medio |
Uso de la superficie | 3 | Bastante bueno, dado el pequeño tamaño de los pasillos. La utilización del volumen es ineficiente. |
-
Racks de varias plantas
Este sistema de almacenamiento responde a los mismos principios que el anterior ya que, en la práctica, se trata de dos o más bodegas de una planta instaladas una encima de la otra. Con ello se logra una mayor capacidad de almacenamiento al disponer de racks más altos dotados de entrepisos (que, al fin y al cabo, vendría a ser como disponer de varias plantas físicas).
Con este sistema se elimina la necesidad de utilizar escaleras manuales o carritos-escalera y se consigue, por lo tanto, una disminución relativa del tiempo empleado por cada artículo recogido o depositado.
En las bodegas con este sistema es imposible el empleo de medios mecánicos, excepto en la planta inferior o en los altillos de alta resistencia (que tienen, eso sí, un mayor costo de instalación). Pueden usarse, sin embargo, grúas elevadoras u otros medios, como ascensores o grúas para la alimentación a las plantas superiores con pallets completos.
- Calificación de este sistema:
Parámetro | Calificación | Comentario |
Costo total de la inversión | 1,5 | Ligeramente superior a las bodegas de una sola planta. |
Costo de manipulación | 9 | Superior a las bodegas de una sola planta. Es imposible utilizar métodos mecánicos en la colocación y picking de las plantas superiores (su uso supone una mayor inversión). |
Capacidad de manipulación | 3 | Inferior a las bodegas de una sola planta, ya que se ralentiza la operación en las plantas superiores al no usar medios mecánicos en ellas. |
Uso de la superficie | 5 | En uso de superficie es similar a las bodegas de una sola planta, pero en volumen los duplican o triplican. |
-
Racks sobre bases móviles o Movirack
El sistema de racks móviles o Movirack ahorra gran cantidad de espacio, ya que el número de pasillos queda reducido, generalmente, a uno solo. Sin embargo, cuando la utilización de los racks es muy frecuente o si el número de racks es muy grande, se pueden diseñar sistemas con más de un pasillo, mediante la agrupación de los racks en varios bloques.
La colocación y recogida de los productos se lleva a cabo de forma exclusivamente manual y, dado que las distancias que se deben recorrer son mucho más cortas que en el caso de los sistemas de racks fijos, el tiempo que se necesita para abrir el pasillo (o los pasillos) queda ampliamente compensado.
En estos sistemas en los que los racks quedan herméticamente cerrados formando bloques, los productos depositados se ven libres del polvo. Además, cuando el movimiento se ejecuta eléctricamente, estos bloques de racks están provistos de un sistema de seguridad que detiene automáticamente la maniobra si aparece algún obstáculo, con lo que se evitan posibles accidentes, como pueda ser el aplastamiento de personal en el interior.
Los sistemas de racks de bases móviles pueden estar controlados por ordenador, de forma que las aperturas y cierres del pasillo pueden ser programados. Con este sistema se agilizan las operaciones.
- Calificación de este sistema:
Parámetro | Calificación | Comentario |
Costo total de la inversión | 3,5 | La inversión será más costosa cuanto más pequeña sea la instalación (en proporción a su capacidad). Se pueden colocar sistemas de racks sobre bases móviles en varios niveles. |
Costo de manipulación | 8 | La facilidad de la apertura y el cierre del pasillo en los sistemas automáticos reduce el tiempo de operación, con el consiguiente aumento de la productividad y el menor costo de la mano de obra por cada artículo recogido o posicionado. |
Capacidad de manipulación | 4 | La reducción del tiempo de operación supone un aumento en el número de artículos posicionados y recogidos por cada unidad de tiempo. |
Uso de la superficie | 7 | El reducidísimo número de pasillos que precisan estas instalaciones incrementa considerablemente el índice de utilización del suelo. Éste incluso puede ser mayor con la instalación del sistema en varios niveles, aunque eso conlleva un considerable incremento de la inversión y no se aprecia, como contrapartida, una incidencia favorable sobre el costo y la capacidad de manipulación. |
-
Bodegas de pasillos estrechos
Dentro de los sistemas que responden al principio de hombre a producto, las estructuras de almacenamiento con pasillos estrechos son las que presentan mejores índices en cuanto a utilización del suelo, capacidad de manipulación y costo de manipulación. Por contra, el costo de la inversión de esta modalidad es superior a las anteriores, aunque se mantiene en niveles aceptables.
El espacio ocupado en la superficie queda altamente restringido con la disposición de pasillos de separación entre las cargas muy reducidos que pueden llegar a ser de 1.000 mm. No obstante, lo más corriente es habilitar pasillos de entre 1.500 y 1.700 mm de anchura para poder utilizar cargas completas. Este sistema permite aprovechar toda la altura total de la bodega hasta el mismo techo.
Los medios de manutención empleados son exclusivamente mecánicos como por ejemplo grúas tipo torre, trilaterales, order picker para niveles altos o transelevadores manuales, todos ellos explicados en la sección que trata los equipos de manutención. En estos sistemas es imprescindible alcanzar un alto nivel de racionalización para lograr la capacidad máxima, por lo que la utilización de transportadores de rodillos, transpaletas, grúas e incluso vehículos autoguiados y láserguiados (AGV y LGV) son importantísimos para lograr este objetivo.
Otro aspecto fundamental a tener en cuenta es conseguir una posición correcta de trabajo durante las operaciones de recogida y depósito de las mercaderías en los racks. El operador debe poder moverse, tanto vertical como horizontalmente entre los racks y así poder realizar operaciones ergonómicamente correctas y, por lo tanto, eficaces y seguras.
Además, tiene a su disposición otros aliados fundamentales para lograr unos altos índices de productividad. Entre ellos, destacan la integración de un buen software de gestión de bodegas (WMS) y el uso de terminales de radiofrecuencia que faciliten las secuencias de operación correctamente y que, entre otras cosas, permitan a cada operario manejar diversas órdenes de pedido simultáneamente.
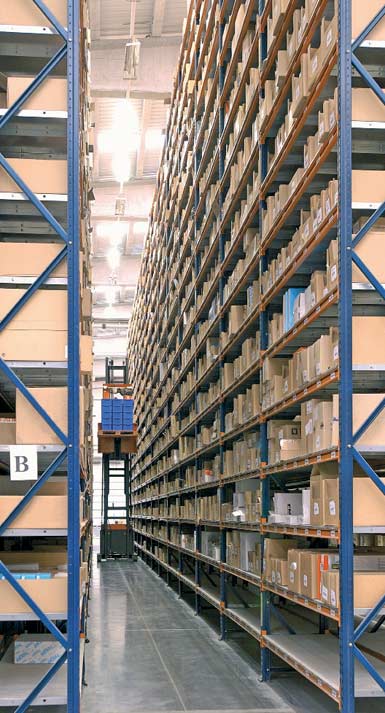
Ejemplo de bodega con pasillos estrechos
- Calificación de este sistema:
Parámetro | Calificación | Comentario |
Costo total de la inversión | 3 | La inversión alcanza unos índices batante altos, pero pueden ser asumibles por la mejora de los demás parámetros. |
Costo de manipulación | 2 | Al realizarse toda la operación con ayuda de elementos mecánicos, la incidencia del costo de la mano de obra se reduce. |
Capacidad de manipulación | 5 | Este factor crece espectacularmente, dada la agilidad de movimientos que se consigue con el sistema. |
Uso de la superficie | 6 | Este índice es altísimo gracias a la utilización de pasillos muy estrechos y el aprovechamiento de toda la altura de la bodega. |
-
Racks dinámicos de picking
Dentro de la estrategia de hombre a producto, el sistema de preparación sobre piezas pequeñas con el que se obtiene un más alto rendimiento es aquel que se basa en el uso de racks dinámicos.
Cada una de las cajas que dan al pasillo de preparación consta de una referencia y detrás de ellas se encuentran las de reserva. El número de pasillos necesarios en una instalación se reduce considerablemente, así como el recorrido que cada operador ha de realizar.
Gracias a esa ubicación mínima de espacios reservados para pasillos, el aprovechamiento de la superficie es mucho más alto que en otro tipo de sistemas.
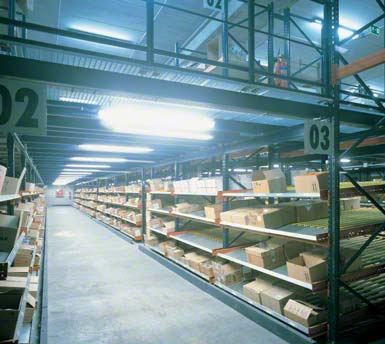
(A) Bodega para empresa de venta en aeropuertos
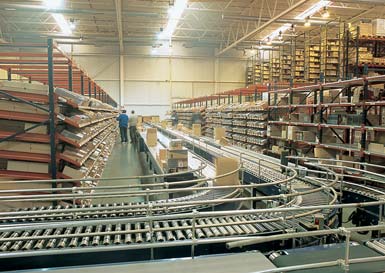
(B) Bodega para productora discográfica
La preparación de los pedidos se puede realizar según tres modalidades:
- La más simple de ellas es utilizar un carro (o una preparadora de pedidos) con el que el operario recorre el rack y va conformando el pedido.
- La segunda posibilidad consiste en habilitar unos transportadores en uno de los lados del pasillo, adosados a uno de los racks.
- La tercera opción también emplea transportadores, pero estos se instalan en el centro del pasillo. En este caso, se prioriza la operatividad sobre la capacidad de almacenaje (como podemos ver en la Imagen B sobre estas líneas).
Las distintas soluciones estructurales disponibles permiten adaptar los racks dinámicos para picking a distintas necesidades. Por ejemplo, se pueden habilitar los niveles altos para alojar pallets con mercadería de reserva e incluso combinar el picking dinámico sobre caja y sobre pallet.
Estos sistemas se pueden mejorar, aumentando considerablemente el número de operaciones, con la instalación de pick-to-light, que indica de dónde y en qué cantidad se ha de extraer cada referencia. El sistema de gestión es el encargado de administrar y controlar estos dispositivos.
Los sistemas de picking sobre racks dinámicos son fundamentales cuando se necesita preparar muchos pedidos y con muchas referencias. Si, además, se les acoplan dispositivos pick-to-light, están muy cerca de lo que se considera picking automático o de producto a hombre. De hecho, para productos de gran consumo, es frecuente instalar estos sistemas junto a un miniload o a carruseles horizontales. En estos casos, el picking dinámico se gestiona como parte de estos recursos automáticos.
- Calificación de este sistema:
Parámetro | Calificación | Comentario |
Costo total de la inversión | 8 | El costo de la inversión es medio (ya que aunque es de un 8, se compensa con las ventajas y eficiencia que se aporta). |
Costo de manipulación | 2 | El costo de manipulación es muy bajo, dado que con el sistema se mejora la eficiencia del personal disponible. |
Capacidad de manipulación | 8 | Muy alto en entornos con un gran número de operaciones, especialmente si se usa pick-to-light. |
Uso de la superficie | 8 | Muy alto por el reducido número de pasillos. La utilización de la altura es ineficiente, salvo que se use el espacio por encima de los racks de picking con pallets de reserva. |
2. La estrategia de producto a hombre
Este principio, totalmente opuesto al que se basa en el hombre al producto, trata de acercar las unidades al operario, de tal manera que este tenga que moverse lo mínimo indispensable. Con esta forma de trabajar, se eliminan los tiempos muertos que se producen en el traslado de una a otra posición de colocación o recogida.
A diferencia de los sistemas vistos anteriormente, tanto la colocación del producto en posición como su extracción se realiza de manera manual, prácticamente, aunque el grado de automatización en el movimiento de las unidades es casi total.
Los sistemas de almacenamiento que usan esta estrategia son los transelevadores miniload, el almacenamiento vertical y los carruseles horizontales.
-
Transelevadores de cajas (miniload)
El miniload es, básicamente, una bodega compacta alimentada por un transelevador de forma totalmente automática. Las unidades que estos sistemas manejan son cajas o cestones, que suelen medir 600 x 400 mm u 800 x 600 mm y están adaptados al tamaño de las piezas que contienen.
Este sistema también puede manipular bandejas en lugar de cajas, con las que se pueden ubicar diferentes productos de muy pequeñas dimensiones de una sola vez, formando así una mini unidad de carga. De hecho, de ahí deriva su nombre: miniload.
Esta opción de almacenaje requiere muy poca superficie y, dado que responde al principio producto al hombre, permite la configuración de puestos de trabajo ergonómicos y muy eficientes. De hecho, los miniload incluso pueden combinarse de forma que un único trabajador pueda atender varios aparatos simultáneamente.
La carga máxima que maneja este sistema es de unos 100 kg por unidad (caja, contenedor o bandeja) y alcanza altas velocidades de elevación (hasta 90 m/min), así como de desplazamiento horizontal (hasta 250 m/min).
En estos sistemas una de las ventajas más importantes es el control del stock. Normalmente los artículos son identificados por medio de códigos de barras leídos por escáneres. El sistema informático que incorpora el miniload realiza tanto el control y la gestión de la mercadería, como las operaciones que se deban llevar a cabo.
A la hora de hablar de los miniload, se ha de tener en cuenta que se pueden encontrar distintas configuraciones de los elementos de este tipo de bodega automatizada con diversas capacidades y velocidades. Eso permite adaptar la solución a las necesidades de cada empresa o industria.
En concreto, los miniload pueden clasificarse según su rendimiento en tres tipos: medio, alto y muy alto.
- Los miniload de rendimiento medio son los que pueden mover un máximo de 150 cajas por hora (75 de entrada y 75 de salida) en un ciclo combinado (se aprovecha el movimiento de inserción de una unidad para extraer otra o viceversa). Al igual que en los transelevadores de pallets, un lateral de los racks que aloja la carga puede incorporar niveles dinámicos inclinados para hacer picking sobre los productos de rotación A por un pasillo paralelo, mientras que las referencias de rotación B y C se sirven por la cabecera del miniload. Además, se pueden habilitar dispositivos pick-to-light y put-to-light para acelerar aún más la operativa.
- Los miniload de alto rendimiento pueden mover entre 150 y 180 cajas por hora de entrada y la misma cantidad de salida en ciclos combinados. Al igual que los anteriores, pueden incorporar niveles de racks dinámicos en un lateral. También son adecuados para instalar varios puestos de picking en la cabecera si se estima conveniente. En estos sistemas es imprescindible la colocación de dispositivos pick-to-light y putl-to-light.
- Por último, se encuentran los miniload de muy alto rendimiento, que son capaces de superar las 250 cajas por hora de entrada y 250 de salida en ciclos combinados. En estos modelos solo se suministran las cajas por cabecera, generalmente, y los puestos de picking pueden establecerse en una zona anexa. En estas bodegas es esencial contar con medidas de ergonomía y sistemas de ayuda muy intuitivos, así como un software de gestión y control avanzado. Debido a sus características, los miniload de muy alto rendimiento son una buena solución para extraer muchas cajas en períodos de tiempo muy cortos. Por esto, su uso puede resultar óptimo para bodegas temporales de pedidos preparados (búfer), bodegas de alimentación de puestos de montaje o manipulación y como secuenciador para entregar las cajas ordenadas de una forma rápida.
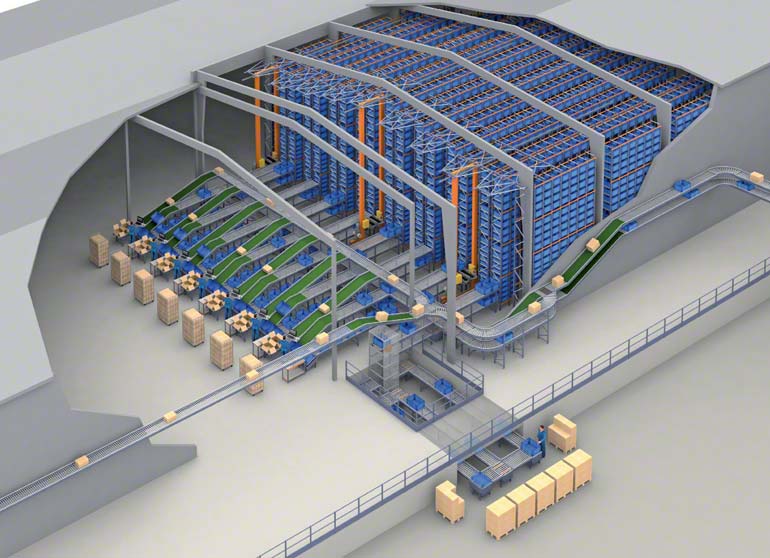
Bodega automatizada para cajas miniload de muy alto rendimiento
- Calificación de este sistema:
Parámetro | Calificación | Comentario |
Costo total de la inversión | 7 | Intermedio con tendencia a alto. |
Costo de manipulación | 1 | Al tratarse de un sistema casi automatizado por completo, la influencia del costo de la mano de obra en la manipulacion es prácticamente nula. |
Capacidad de manipulación | 6 | El índice de capacidad de manipulación es medio, con tendencia a alto-muy alto, dependiendo del modelo. |
Uso de la superficie | 8 | La capacidad de almacenaje es muy elevada en relación a la superficie de suelo utilizada. Puede ocupar toda la altura de la bodega. |
-
Sistemas de almacenamiento vertical y los carruseles horizontales
Aunque en la actualidad el sistema más utilizado es el miniload, todavía podemos encontrar soluciones como las bodegas verticales automáticas o los carruseles:
-
La ventaja principal que presentan los sistemas de almacenamiento vertical es el mayor aprovechamiento del espacio disponible en dirección vertical, es decir, la altura. Están especialmente indicados en situaciones en las que la superficie disponible es limitada pero sí se puede construir hacia arriba. Se trata de estructuras cerradas que acercan el producto al operario para que este lo manipule.
-
Los carruseles (tanto los verticales como los horizontales) utilizan un sistema mecánico en su interior para llevar la mercadería hasta el operario, que es el encargado de extraerla sin tener que moverse de su puesto.
Estos sistemas de almacenamiento vertical y horizontal actualmente están en desuso, pero es interesante conocerlos porque en algunas bodegas todavía se utilizan. Para más información, tiene a su disposición este artículo enteramente dedicado a ellos.