Se denomina máquina de recorrido fijo a los dispositivos o máquinas (normalmente, automáticas) que se utilizan en una bodega y que, permanentemente, realizan un mismo recorrido sobre un circuito prefijado. Dentro de esta categoría están incluidos los transportadores, las electrovías, los vehículos de guiado automático (AGV y LGV) y, por supuesto, los transelevadores.
No pueden incluirse en este grupo los demás vehículos utilizados habitualmente en una bodega, como por ejemplo, las grúas de cualquier tipo. Las torres trilaterales guiadas o filoguiadas, pese a tener unos recorridos más o menos prefijados en el interior de la bodega, tampoco pertenecen a esta clasificación, ya que pueden circular libremente por este sin restricciones si así se desea.
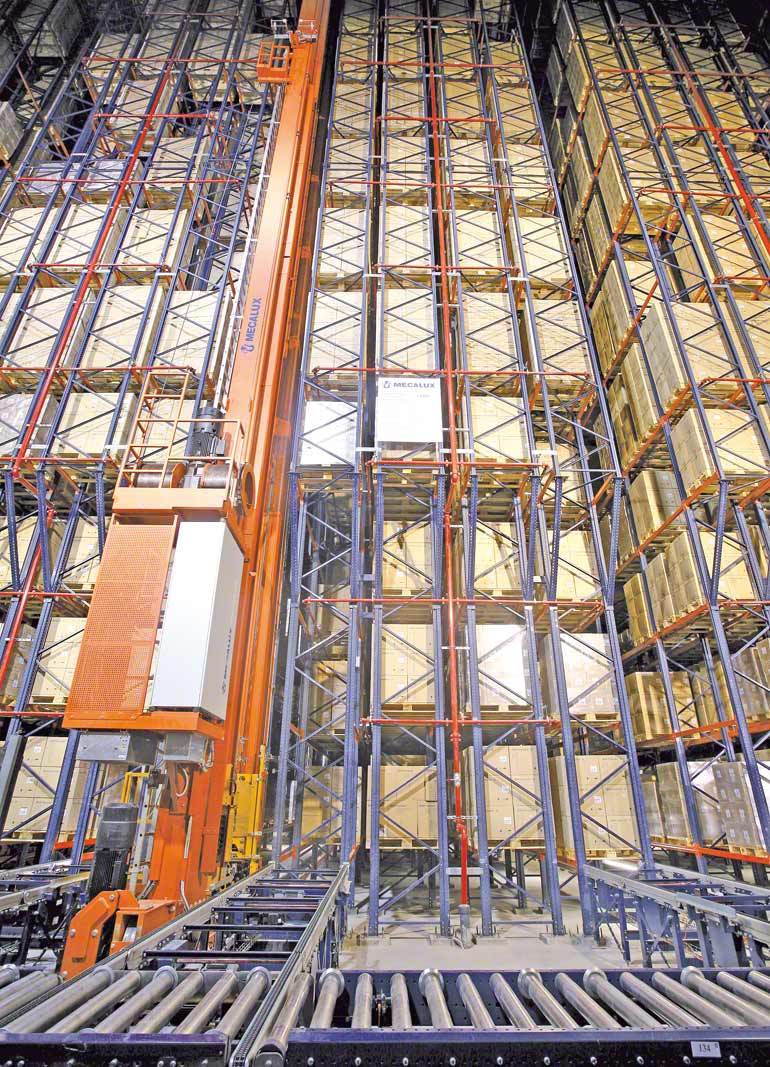
Bodega autoportante dedicada al sector farmacéutico
Las máquinas de recorrido fijo son las ideales para ser utilizadas dentro de una bodega autoportante, pero es conveniente precisar de qué manera podemos conseguir su máximo rendimiento.
Precisión del posicionamiento
Los distintos sistemas de esta familia disponen de elementos que garantizan, en todo momento, su correcto posicionamiento en la instalación o entre los racks. Así, por ejemplo, los transelevadores disponen de telémetros láser, sistemas electrónicos de parada, dispositivos de detección dinámica para posicionado fino, etc.
Estos aparatos actúan como ojos y oídos del sistema automático, de manera que, en todo momento, las máquinas se posicionan a la perfección y son capaces de manejar la carga sin golpearse ellas mismas ni a la mercadería, contra los racks. También son capaces de, por ejemplo, detectar si un hueco ya está ocupado o si hay algún obstáculo que impida su desplazamiento. Estos sistemas de posicionamiento son indispensables para construir con seguridad autoportantes de gran altura.
Apoyo de los elementos de recorrido fijo
Los apoyos de los aparatos de recorrido fijo están diseñados en función de las características específicas de cada uno de ellos. Por ejemplo, los transportadores de rodillos se apoyan sobre caballetes anclados al pavimento. Los transelevadores lo hacen sobre dos raíles, uno que se ancla al suelo y el otro, al arriostramiento superior de los racks.
A continuación procederemos a exponer cada uno de ellos para explicar sus características propias.
Apoyo de los transportadores de rodillos
Los transportadores de rodillos se adaptan a las características del ciclo de trabajo y al recorrido fijo que han de efectuar las mercaderías que mueven. Para ello, están formados principalmente por tramos rectos, que pueden bifurcarse mediante diversos tipos de derivaciones estandarizadas. Además, existe la posibilidad de comunicar unos y otros cuando están colocados en distintos niveles de altura, mediante el uso de elevadores.
Estas máquinas se fabrican en tramos estándar con longitudes variables de entre 1,5 y 3 m, por lo que, en función de las características del pavimento y del peso del tramo y de la carga, se instala, como mínimo, un caballete de soporte en cada uno de sus extremos. Estos soportes se atornillan al suelo por medio de placas de apoyo graduables.
En ocasiones, los transportadores se colocan en puntos en los que se concentran cargas procedentes de diversos orígenes de la propia bodega, por lo que se precisa de un anclaje más o menos especial, en función del peso total de la agrupación de elementos de transporte, así como de las cargas.
Apoyo de los transelevadores
Por su parte, los transelevadores necesitan de otros apoyos dada su altura. Se utilizan dos raíles, uno anclado al pavimento y otro, al arriostramiento superior de los pasillos de los racks.
- El raíl inferior ha de tener una resistencia muy elevada, teniendo en cuenta que, en una máquina de este tipo, las cargas que se transmiten a cada rueda pueden superar las 18 t. Las guías inferiores que se utilizan tienen unos 150 mm de altura y están provistas de zapatas soldadas de 250 x 150 mm que se instalan a lo largo del raíl cada 450 mm. Estas zapatas se anclan al suelo por medio de cuatro tornillos, dos fijos y otros dos niveladores; estos últimos están dotados de una tuerca y una contratuerca y tienen un recorrido por debajo del nivel del suelo de unos 150 mm aproximadamente.
- Por otra parte, en los transelevadores de gran alcance –que son los que habitualmente se utilizan en las bodegas autoportantes–, la fijación del raíl superior se realiza en los arriostramientos más altos de los racks, ya que en el edificio no existe ninguna otra estructura por encima de esas (incluso la cubierta va unida a los racks).
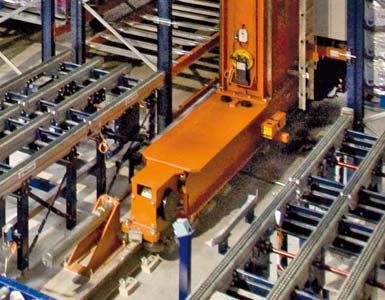
Detalle de un testero o bastidor inferior de un transelevador y de un carril de rodadura
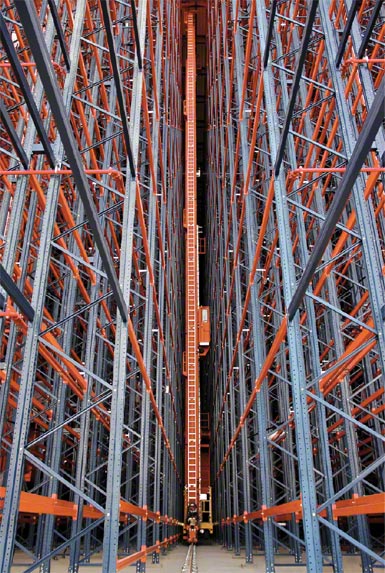
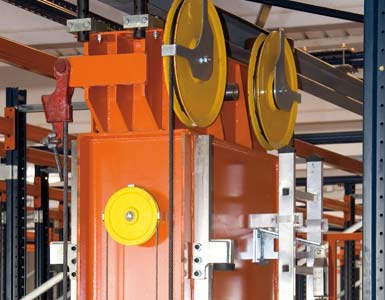
Testero superior de un transelevador y carril superior
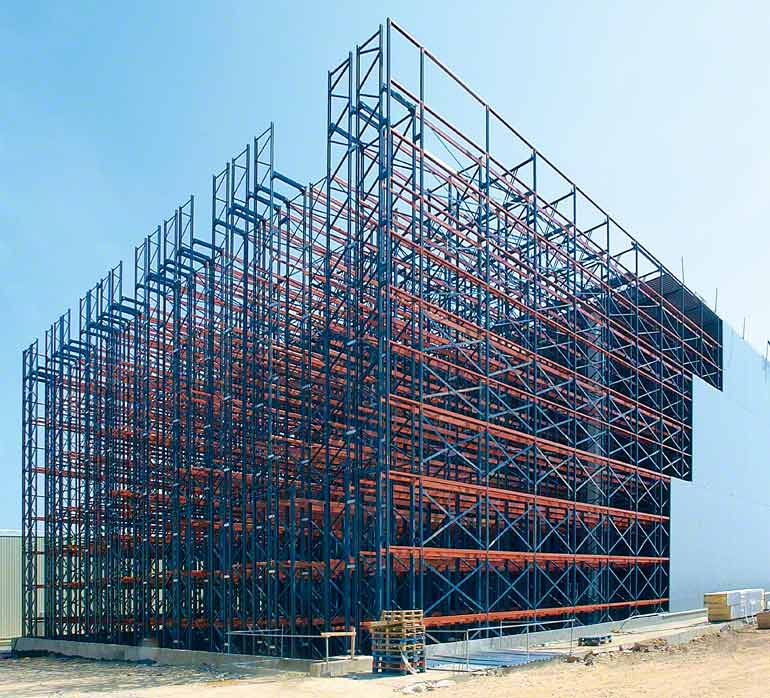
En una autoportante, los racks configuran la estructura del propio edificio
Holguras para los aparatos de recorrido fijo
En las bodegas autoportantes los márgenes de trabajo son muy reducidos y prácticamente se trabaja con márgenes de pocos milímetros. Por eso es muy importante poder precisar cuáles son las holguras mínimas a las que el diseñador tiene que ajustarse.
A efectos de diseño, los puntos críticos a los que hay que prestar la máxima atención en cuanto a las holguras son los pasillos de trabajo, los niveles de carga y el posicionamiento longitudinal de las cargas.
Holguras en los pasillos de trabajo
El ancho que debe tener un pasillo de trabajo, en una bodega autoportante, se determina en función del espacio de circulación que necesita el transelevador que se moverá por él y del ancho de las cargas que deberá transportar.
Dado que estas máquinas van guiadas tanto por su extremo superior, como por el inferior, las posibilidades de desviarse de su camino son prácticamente nulas. Tan sólo existe un riesgo calculado de pandeo, producido por la gran altura de estos aparatos. Por lo general, este pandeo ha sido previamente calculado por el fabricante, que habrá puesto los medios necesarios para evitarlo.
Posicionamiento de las cargas en los racks
La mayor contingencia que puede producirse en el interior de una bodega se suele deber a los posibles desplomes de las cargas. En este sentido, se puede dar el caso de que alguna de las mercaderías sobresalga del rack y ocupe más espacio del que se había previsto.
La correcta definición de las características de las unidades que se almacenarán en la instalación, antes de su diseño, y un escrupuloso respeto de las normas de seguridad y de uso de las máquinas, una vez en funcionamiento, son las recetas para evitar este tipo de problemas. Determinar las holguras relativas al posicionamiento de las cargas es una cuestión de vital importancia en este punto.
Las holguras son las distancias que hay que considerar entre las unidades de carga y los elementos del rack y se especifican en relación a la medida total de dichas unidades, incluyendo cualquier saliente que puedan presentar.
En función del peso de las mercaderías y de la altura de la bodega proyectada se puede optar entre colocar dos o tres unidades en sentido longitudinal dentro de cada alveolo.
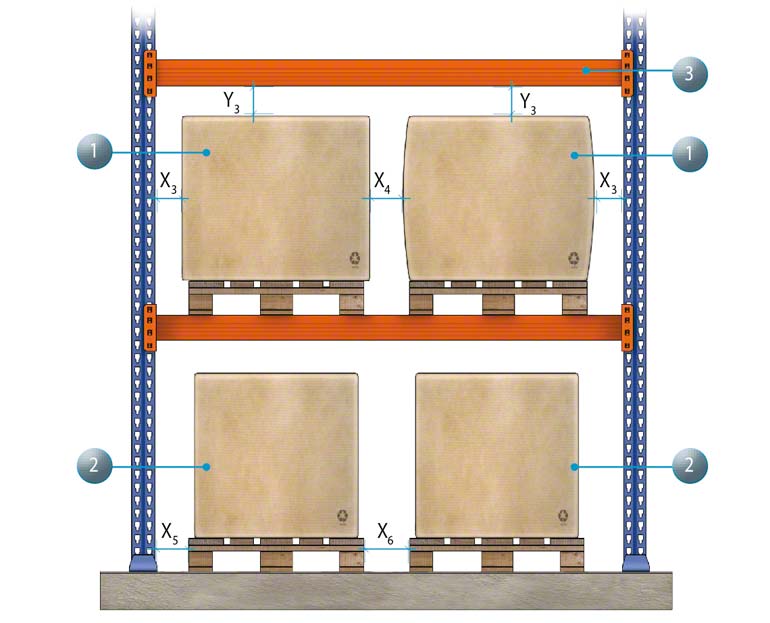
Detalle de holguras en un módulo.
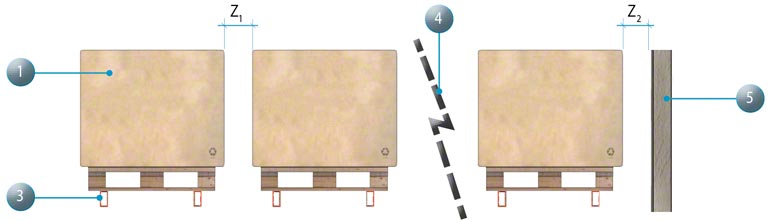
Detalle de holguras en fondo
En los esquemas que acompañan a estas líneas se representan las holguras, tanto en el módulo como en el fondo, para el caso de dos pallets por módulo. Las claves de las medidas representadas por letras (X1, X2...) se definen en otras tablas a continuación.
Las holguras mínimas que se tienen que respetar se definen en la norma EN 15620 y se aplican en función de la clase de rack que se esté proyectando (clase 100, 200, transelevadores, o clase 300, grúa hoquilla torre, o clase 400, grúa hoquilla retráctiles y contrapesadas).
Holguras mínimas para la clase 400 | ||||
Altura desde el suelo hasta el nivel del larguero (mm) |
Holguras en el módulo | Holgura en fondo | ||
Horizontales X3, X4, X5, X6 (mm) |
Verticales |
Z1 (mm) | Z2 (mm) | |
3.000 | 75 | 75 | 100 | 50 |
6.000 | 75 | 100 | ||
9.000 | 75 | 125 | ||
13.000 | 100 | 150 |
Holguras mínimas para la clase 300 (300A y 300B) | |||||||
Altura desde el suelo hasta el nivel del larguero (mm) | Holguras en el módulo | Holgura en fondo | |||||
Horizontales X3, X4, X5 y X6 |
Verticales |
Z1 (mm) | Z2 (mm) | ||||
300A | 300B | 300A | 300B | 100 | 50 | ||
3.000 | 75 | 75 | 75 | 75 | |||
6.000 | 75 | 100 | |||||
9.000 | 75 | 125 | |||||
12.000 | 100 | 150 | |||||
15.000 | 100 | 175 |
En las instalaciones de las clases 100 y 200, las holguras están definidas en función de múltiples parámetros, como son las dimensiones de las unidades de carga, la altura de la bodega, la disposición en simple o doble fondo y los dispositivos del transelevador. Por todo ello es preciso desarrollar un proyecto individual para definir las holguras en cada caso particular. No obstante, en la siguiente tabla se indican, a título orientativo, las especificaciones mínimas para el caso de una bodega de profundidad simple.
Holguras mínimas para la clase 100 y 200 | |||||
Holguras en el módulo | Holgura en fondo | ||||
Horizontales | Verticales | Z1 (mm) | Z2 (mm) | ||
X3, X5 (mm) | X4, X6 (mm) | Y3 (mm) | |||
75 | 90 | 85 | 100 | 75 |